La UCO crea una nueva tecnología que reduce hasta un 50% la huella de carbono en los prefabricados de hormigón
Ciencia
El proyecto Precast-CO2 de la Escuela Superior de Belmez explora un nuevo sistema de curado de prefabricados de hormigón que captura dióxido de carbono en el interior del propio elemento
La Universidad de Córdoba destina el 17,9% del presupuesto de 2025 a investigación
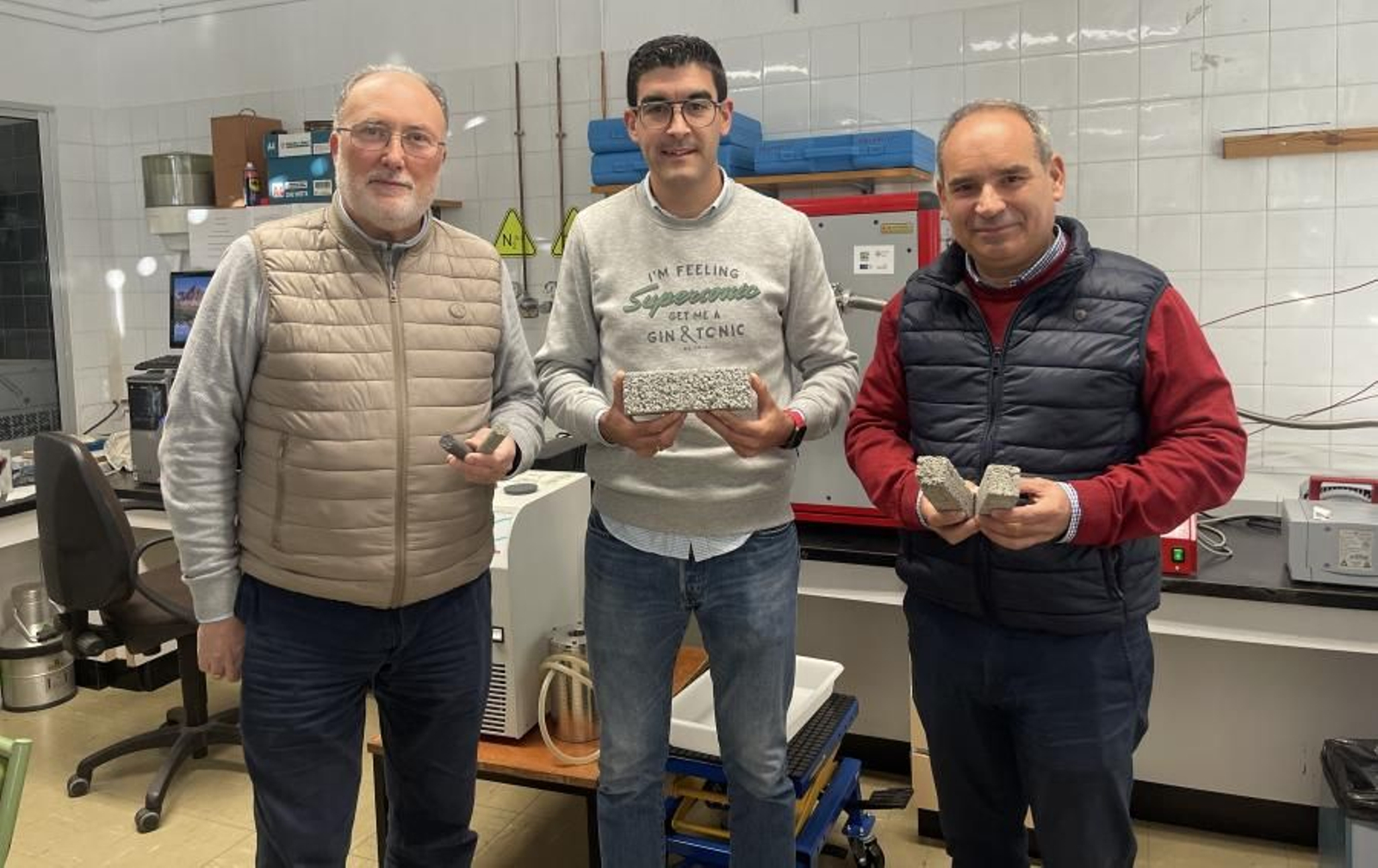
Belmez/El hormigón es el segundo producto más consumido a nivel mundial después del agua, pero el uso de este material que en buena medida ha ayudado a construir el mundo moderno tiene un alto coste para el medio ambiente. Según la Agencia Internacional de la Energía, el 8% de todas las emisiones globales de dióxido de carbono están relacionadas con la producción del cemento.
El proyecto Precast-CO2, con base en la Escuela Politécnica Superior de Belmez de la Universidad de Córdoba, ha estado buscando la manera de reducir el impacto medioambiental de esta industria, y tras cuatro años de investigaciones, ha conseguido demostrar que la tecnología de curado con CO2 es capaz de reducir hasta un 50% la huella de carbono en la fabricación de productos prefabricados de hormigón.
“Durante la fabricación de cemento se calcina carbonato cálcico, un proceso que emite a la atmósfera grandes cantidades de dióxido de carbono”, explica José Ramón Jiménez, uno de los investigadores responsables del proyecto. Ahora, este trabajo ha desarrollado un nuevo proceso que permite capturar parte de este gas e incorporarlo durante el proceso de curado en el interior de elementos prefabricados de hormigón, como adoquines, bordillos o bovedillas.
Cuando el dióxido de carbono se convierte en piedra
Para ello, explica el investigador, la pieza de hormigón se introduce en su etapa inicial en cámaras con una concentración de dióxido de carbono muy superior a la de la atmósfera. De esta forma, la portlandita, una fase mineral que se forma durante el proceso de hidratación del cemento interacciona con el CO2 formando carbonato cálcico, un reacción más conocida como carbonatación.
Tal y como subraya David Suescum, otro de los investigadores que ha desarrollado su tesis doctoral en el proyecto, una de las grandes ventajas es que este carbonato cálcico que se genera a partir del dióxido de carbono endurece el material, cerrando sus poros y rellenando las pequeñas fisuras, mejorando así sus prestaciones y resistencia a la presión. De hecho, y según los resultados de la propia investigación, “en tan sólo 24 horas se logran alcanzar las mismas resistencias mecánicas que se obtienen curando el hormigón al aire libre en 28 días”.
En busca de nuevos captadores de CO2
Para realizar todo este proceso, el proyecto, que ha contado con la colaboración de las empresas cordobesas como Pavigesa y Gecorsa, se ha lanzado a la búsqueda de nuevos materiales captadores de dióxido de carbono para incorporarlos al hormigón.
Algunos de ellos se conocen como hidrotalcitas o PMOs, capaces de absorber 0,9 gramos de CO2 por gramo de material, o lo que es lo mismo, una cantidad casi equivalente a su propio peso. “Al emplear uno de estos materiales en el revestimiento de una casa unifamiliar en uno de nuestros ensayos, logramos capturar todo el dióxido de carbono presente en un volumen equivalente al de tres estadios de fútbol como el Santiago Bernabéu”, explica José María Fernández, otro de los investigadores responsables.
El proyecto supone de esta forma un paso importante en la economía circular de los productos prefabricados de hormigón, mediante una nueva tecnología que, según afirman sus investigadores, “podría estar ya lista para usarse a nivel industrial”. En el horizonte, se sitúa el ambicioso objetivo de la Unión Europea de reducir para el año 2040 las emisiones netas de gases de efecto invernadero en un 90%, un propósito que requerirá, ineludiblemente, desarrollar nuevos sistemas de captura y almacenamiento de dióxido de carbono.
También te puede interesar